Chapter II: The frame
1. We must begin with this part, because its design has the most substantial influence on the character of the work, all of its parts and even the form of the casing. A watch, and possibly other machines which consist mainly of turning parts, requires a frame to support both ends of each arbor, and this frame has to satisfy the same general requirements as in any other machine.
2. If we examine the frame of a number of different watches we can differentiate between three kinds of construction:
full plate,
three-quarter plate, and
the frame with bridges.
We first want to compare these three systems to select that which offers the greatest advantages for production and the best conditions for strength and good service of the watch.
3. Bridge work is used almost exclusively in Swiss watch production and we must realise that it is more than any other calculated to reveal the watch mechanism advantageously to the eye and to bestow a luxurious appearance to the works. (notes: 1) On the other hand, it is more complicated and cannot be produced and finished for the same price and in the same time as a full or three-quarter plate frame. The same can be said for taking apart and assembling, and it is probable that workers, both in production and repair work, would object to this system if it were introduced now, instead of it having been sanctified by practice over a long period.
4. The bridge frame for a cylinder watch requires 10-11 screws for the bridges, and 16 steady pins; the three-quarter plate frame needs only 7 screws and 6 steady pins. In manufacture, the preparation and fitting of the three pillars are to be balanced against the preparation and fitting of 3-4 screws and 9-10 steady pins; an undeniable advantage in favour of the three-quarter plate if we have cheap and rapid production in mind. Besides, 4 bridges have to be made instead of an upper plate, and the consideration for making and finishing these numerous parts shows a substantial saving in favour of three-quarter plate frames.
For the repairer the same inconveniences occur; the number of individual parts with bridge work is too large and necessarily requires a greater time to take apart and assemble.
5. The stability of the escapement and the uprightness of pinions is endangered each time a steady pin in a bridge movement is bent. For this reason some of the best Swiss manufacturers omit the bridge of the third wheel and place its hole on the centre wheel bridge; because this wheel, which is furthest from the surface of the plate, can suffer most from the last-mentioned danger. It is strange that the same causes did not lead to a complete change to the system.
6. It is stated that an advantage of bridge work is that it is simpler to take out certain parts, such as the barrel in the case of a broken mainspring. But often even this small advantage does not really exist because to take out the barrel, if its hole in the plate has little shake or when the steady pins of the barrel bridge are long, the centre wheel must be taken out first; and if there is little room it is often necessary to raise the bridge of the third wheel. Then 4 or 5 screws are to be screwed in, instead of the three screws of an upper plate. Therefore the only remaining advantage of the bridge watch is easier visual examination of the train. (2)
7. Three-quarter plate work is very rarely implemented in Switzerland, but it is used more in England where, for about 20 years, it has enjoyed a clear advantage over the old full plate movement. It ensures the support and uprightness of the arbors better than the Swiss system and requires a smaller number of pieces and less time and trouble when repairing, with sufficient facility for removing escapement parts.
8. However, the layout of the train in these two frames is exactly the same, so that a three-quarter plate movement might possibly be converted into a bridge movement by removing the pillars and the upper plate and replacing them with a bridge for each arbor.
9. In contrast, the full plate movement requires a completely different layout of the train. It is the oldest frame for watches and it was always very much preferred in England. This kind of frame was also generally accepted by the United States watch factories.
10. It offers the opportunity of having a balance of larger diameter than is possible in the other frames, but this is a reason to which no special importance should be attached; it has long been known that an excessively large balance, since it approaches the effect of a fly, is not suitable for exact time measurement. It was probably the reduction in size of the balance which led English manufacturers to change to the three-quarter plate.
Anyway, it is not appropriate to set the balance near the centre of the plate in full plate watches; because when this happens each circular movement of a suspended watch exerts its full influence on the oscillations of the balance. If the balance is moved near the edge of the plate, this influence is minimised.
11. The full plate frame permits a far simpler and roomier arrangement of the train and, particularly in fusee work, the wheels and pinions can be made larger than in a three-quarter plate frame, which is certainly an advantage. But on the other hand, if we want to use a mainspring of the same width the full plate frame requires a substantially greater height for the frame and the case. This was acceptable when fashion required or permitted a case with a strongly curved bottom, but fashion now demands a nearly or completely flat bottom, and from this developed the need to abandon the full plate, since otherwise the case would be too thick.
12. Full plate work is undoubtably the simplest; it can be implemented with only two bridges, (for the balance) and with a work saving no other system offers to the same degree.
13. However, assembling a full plate watch is inconvenient and we can only make it bearable by habit and many years of practice. The bridge which carries the lower balance pivot must necessarily go over the end of the fork or, if it is a cylinder watch, the rim of the escape wheel; and the worker who takes off the upper plate without sufficient care inevitably breaks the lower lever pivot, or the lower escape wheel pivot in a cylinder watch. This very often happens to those repairers who take apart English watches without having previously studied the layout.
Indeed, if we want to avoid an accident of this kind the work must be assembled and taken apart on the upper plate, which is a very awkward method, particularly with fusee watches as we must reset the tension of the mainspring after each disassembly.
It is true that all these objections can be easily overcome if we omit the lower balance bridge and set the lower hole of the balance into the pillar plate. But this would not offer the same certainty of uprightness and endshake of the balance staff.
14. Also, examining the escapement of a full plate watch is not as easy as with differently laid out work. Likewise it is impossible to alter the escapement, to clean it or apply fresh oil without taking the whole movement apart.
15. After we compare the advantages and disadvantages of the three systems above, it is not difficult to draw the conclusion that the full plate movement is unsuitable for watches of our time; and of the two remaining arrangements, the three-quarter plate frame is to be preferred because of its greater firmness and cheapness of production.
16. A small saving in practical execution could be achieved by omitting the two lower bridges; the plate needs to be turned off only a little on the dial side in order to allow room for any unevenness of the dial. Spaces for the barrel and motion work, and even for the lever escapement, can easily be made by turning circular sinks on a lathe.
In the same way a small advantage could be obtained during manufacture of three-quarter plate frames if the pillars were omitted and the upper plate made of sufficient thickness to screw it directly onto the lower plate, whereby it would be secured in position by just three good steady pins. This method can even be recommended for flat watches, since it results in greater firmness. The sinks for the moving parts must be prepared on a lathe. Watches in thin gold cases and made with two full plates in this way would be heavier than if they were made with plates of the usual thickness. Also, setting jewels is not as easy as attaching them to bridges; but by means of suitably designed tools it would not be difficult to insert them directly into the plate.
17. The pillars should not be close to the edge of the upper plate. On the contrary, they will better serve their purpose if they are moved a little inward, because the plate can less easily distort when it is screwed on and the shoulders of the pillars are not precisely made or not exactly square. The two pillars close to the barrel should, if possible, be placed so that a straight line from one to the other passes near the centre of the barrel (Fig. 1 and 2); no matter what, the three pillars must be set the same distance from the centre of the work. The barrel is the container of the motive power, and therefore the frame must be designed so that it possesses the greatest rigidity near it.
18. It is not absolutely necessary to give the plates a particular thickness, but the pillar plate should be thick enough to provide a safe grip for good strong screws, and so that the anchor and escape wheel can be placed a little below the surface of the plate. Also, the upper plate must be turned off to take in the centre wheel, so that it lies with its internal surface level to the plate, and additionally it must provide a solid bearing for the upper pivot of the centre pinion.
According to these requirements a good rule is to make the thickness of the pillar plate in a three-quarter plate frame 0.06 of its diameter. The upper plate should be approximately 0.035 of its diameter. Naturally these conditions refer only to watches of average height (approximately 0.16 or l/6 of their diameter).
A flat watch, which has a weaker mainspring and therefore exerts less pressure on the frame and on the centre pinion pivot, can bear a reduction of these thicknesses.
19. The material of which the frame is made also deserves some remarks. A certain degree of elasticity and hardness is necessary and, in addition, it should oppose the smallest frictional resistance to the movement of pivots and the greatest durability against wear resulting from friction.
20. For this latter reason steel cannot be used. Besides, we could not protect it sufficiently from rust and magnetism would be likely to seriously effect the running of such a watch. However, I want to note here that years ago I saw a good watch which had been made in Leipzig by a clever watchmaker known as Zachariae senior, before jewel holes could be obtained easily and cheaply. He screwed steel bushes into the plate for all the pivots, not excluding the escapement, and these steel holes, which were well hardened and polished, showed no wear and the oil kept remarkably well in them after more than 50 years of service.
21. Brass perfectly fits all the requirements for making the frames of good watches, if it is brought to its greatest hardness and density by sufficient hammering or rolling. If possible, hammering is to be preferred to rolling because the latter method stretches the metal, an effect which is not wanted and does not improve its condition. Rollers of small diameter stretch the material more than large rollers, and I undertook a lengthy set of experiments in order to find the best way to get brass of the greatest density possible. For this purpose I had constructed a small tilt hammer (3) of approximately 3 pounds weight, which made 5-6 impacts in a second and was adjusted exactly parallel to the anvil. I found that a strip of brass worked with this hammer did not show the slightest increase in width or length, proof that the considerable amount of mechanical work done on it had acted exclusively in the desired and useful direction. By comparison, I found a strip which had been reduced by this perpendicular hammering from 1 mm to 0.9 mm thick, equal in elasticity to that of a strip which was reduced from 3 mm to the same thickness by rollers. The latter was stretched to 2.5 times its original length.
From this it unquestionably results that the majority of the work which is done by rollers is used to lengthen the metal, and only a small fraction of the work serves the real purpose. This stretching is a source of great damage to the quality of the metal, not only for the reason that it brings out flaws at the edges of the strip, but also because it causes the smallest faults (blisters or casting holes) to expand two or three times; while perpendicular hammering squeezes them together and minimises these faults. I could not continue my tests on a larger scale, because these were the largest pieces which could be managed by my small tilt hammer driven by a man with a foot wheel and I did not have bigger machines available. But the result led me to the conviction that the normal method for achieving the necessary density and elasticity of brass is completely wrong. I would prefer rough bridges and other parts to be punched out by a stamping press from the usual hard-rolled sheet brass which we buy in shops, and left approximately 10 percent thicker to allow for compression by perpendicular hammering. Then each part would be put on a flat anvil and subjected to the heavy impacts of a drop hammer set exactly parallel to the surface of the anvil. Such a method would have yet another advantage; it would make the two sides of the punched-out piece completely smooth and flat so that it would not require as much finishing as it would if it were rolled in the usual way.
For production on a large scale, a press of the kind used for minting large coins is much to be recommended. If we consider the perfection with which coins and medals are shaped, such a press would probably have no difficulty in making pillar plates, including their sinks and the shoulder for the case, with such perfection that they would require no finishing.
22. The plates of English watches are usually very soft, due to the bad practice of the gilder exposing them to a high degree of heat; I don't know why and, indeed, I know that a very good gold plating can be obtained without any heating. In addition, their upper plates are usually too thin; the screwed jewel settings, where the screw heads are sunk into the plate, give the repairer great trouble because of the low strength of the metal holding the screw threads.
23. For many years there has been an increasing demand for so-called nickel movements. These are mainly made of the alloy German silver which is given the incorrect designation of nickel. There is no doubt that German silver is an excellent metal for watch work because of its elasticity and hardness; about which the reader will find further details in the comparative study which I published in chapter 14 of my prize essay on the free lever escapement. Beautifully smoothed and polished German silver makes a pleasant impression on the eye, and its surface resists atmospheric influences very well, while brass must be protected by gold plating. However, if we handle such work carelessly with sweaty fingers ugly black marks form and it is less resistant in this respect than gilded brass.
In all other aspects German silver does not offer any advantage over brass, and it must be said that it is harmful to the eyes of those who are continually occupied with the completion of these shining, polished works. Anyhow, brass, if it is well worked, is so similar to German silver in physical characteristics that the demand for the latter for watchwork might be regarded as merely a matter of taste.
It must also be mentioned that German silver is somewhat sensitive to magnetism, which does not speak in favour of its use for watches.
Further, experience has taught us that screw threads do not hold as well in German silver if they are not lubricated with grease or oil during repair. Hence we usually find rougher screw threads in good German silver work (deeper and with a stronger upward gradient). Also, in many of these watches the barrel hook and even the barrel cover are made of brass, from which we may deduce that the use of German silver for these parts was unsatisfactory.
notes:
1 I believe the first of these two remarks relates to impressing the customer, despite the second in Art. 6 clearly referring to technical examination. Grossmann is not backward and openly voices his opinions, so this interpretation is perfectly reasonable. However, you may relate it to the observation of depths if you wish. [Trans]
2 See footnote 1.
3 "Schwanzhammer", literally a tail hammer. [Trans]
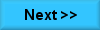