Chapter XII: Keyless Winding (II)
151. This mechanism also incorporates Breguet clickwork; if we attempt to turn the crown the wrong way the clickwork prevents the barrel arbor rotating in this direction and the rounded-off parts of the wheel teeth on the bar slide over those of the barrel arbor wheel, so that no damage to any other parts of the mechanism can occur.
152. In fusee work, as explained already, this mechanism requires yet another arrangement in as much as the wheels of the rocking bar must rest in centrally between the winding and setting positions; this is done by an appropriately attached spring. It is not necessary to use a pusher to bring the rocking bar into contact with the fusee wheel. Here we see one of the surprising effects of friction, which is otherwise a persistent enemy of watchmakers. (16) When the crown is turned in the right direction the friction of the small intermediate wheel on the bar causes the bar to move around the centre of the conical wheel in reaction to the pinion rotating. If this friction is not sufficient to guide the wheel into mesh with the fusee wheel with the necessary certainty, then a small spring washer is inserted under the intermediate wheel in a recess on the lower side of it. If the crown is turned in the wrong direction the wheels freely turn on the rocking bar without any effect, since Breguet clickwork is not used in a fusee watch. For hand setting we use the normal pusher.
153. Beautifully designed rocking bars are made by Mr. V. Kullberg, one the best London watch manufacturers. These have only two wheels and the movement of the bridge results from the very astutely chosen action of the friction of the engaged wheels. The only objection to it is the necessity for a straight pinion and crown wheel, because the bar does not move around the centre of the crown wheel. Mr. Kullberg described his mechanism in the April 1869 issue of the British Horological Journal.
154. After the preceding remarks on the nature of these two main classes of winding mechanism and their essential operation, it remains to say some words about how they are attached to the movement.
The movement drawn in Fig. 43 permits the addition of keyless winding to hunter watches without the any change in the layout of the work, except that the pillars are set somewhat further from the edge of the plate so that the pillar screws are free from the large winding wheels. The lower pivot of the 3rd wheel must be set into the pillar plate and not into a bridge, because the space is used for the minute wheel.
If the winding wheels are to be flush with the upper plate it must be left that much thicker. This is recommended because the increased thickness necessary for the winding wheels can be used to give the arbors of the train greater length (Art. 60). In other respects the layout of the movement and the size of its parts are the same whether the watch is key or pendant wound.
Figure 43.
155. The pendant is the most suitable place on the case for winding, but if it is to be used in an open-face watch then the layout presents some difficulties. The pendant of an open-face watch always corresponds to XII on the dial. If the watch is to have a seconds hand on an eccentric seconds dial, which is the general rule for watches of our time, then the position of the barrel in relationship to the pendant can only be changed within very clearly defined limits, if we want to avoid substantial deviations from the valid principles for the layout of the train (Art. 53).
156. Different methods were adopted in order to avoid this difficulty; and no another aspect of the watch shows, in such a clear way, the need for the manufacturer to subordinate his better judgement to the tastes and habits of the public. If we want to make an open-face keyless watch without seconds, then the problems immediately vanish, because the position of the barrel can be chosen with complete freedom. But the public requires watches with seconds.
In well laid out movements (Fig. 43) the angular distance between the pendant and the barrel centre is approximately 20°, while with the same movement in a hunter case (whose pendant is at III on the dial) this angle is 90° - 20° = 70°, so that a very convenient space for mounting winding wheels results, whereas 20° is much too small for this purpose.
For a long time attempts were made to arrange the dial in another way and the seconds circle was placed, for instance, at VIII or IX; but public taste rejected these changes, although they completely satisfied construction criteria. Symmetry of the dial was an absolute necessity.
In this difficult situation some manufacturers had the ingenious idea of artificially correcting the symmetry of the dial by adding a day hand, whose circle took up a symmetrical position with the seconds circle; but the increased cost of the dial and the additional motion work, for which there was no substantial need, were significant objections to it.
Others provided the train with an extra 4th pinion which only served to carry the seconds hand. This system created sufficient space between the pendant and the barrel for keyless work with the seconds dial in its usual place; but we must complain all the more, as it not only loads the train with a further arbor, but also increases friction because of the small spring which this pinion must have in order to avoid jerks of the hand caused by tooth shake.
157. It is possible to somewhat increase the angle mentioned above by using substantially smaller train wheels. With the common models of Swiss production this angle is often increased up to 30° or even 35° by using much smaller wheels than should be the case for the space made available by the proportions of the frame. A further increase could be achieved if we brought the 3rd wheel closer to the barrel, so that it runs under the toothed edge of it but just far enough away that it does not affect the cylindrical part. But with all these different efforts and the constructional faults contained in them, it is not possible to obtain sufficient space for the winding parts.
158. In order to attain this aim it was necessary to take a step of great boldness which, although it offended against the principles of a good and clean design, was considered satisfactory by watchmakers and manufacturers in the absence of a more favourable solution.
It consists of mounting the 3rd wheel and its arbor against the barrel, whereby the necessary space for the 3rd wheel must be found over the centre wheel. The disadvantages of this layout are apparent. The increased height of the frame required by placing the wheels on top of each other, and the cramped accommodation of three of the largest mobile parts, one over the other, are certainly very serious doubts. But a watch is, more than many other articles, dependent on the dominant taste and its construction must be subjected to the tyranny of fashion; and this fact explains why nearly all open-face keyless movements are laid out in this way (Fig. 44).
Figure 44.
It must be said in favour of this method that all parts of the winding work are unchanged and can be used in open or hunter watches, and that all parts of the train can be made the same regular diameter, as in a watch of the same size with key winding.
159. To overcome the difficulties in the design of open-face keyless watches we must look for a solution using another method of transmitting the winding force. So long as flat, conical and crown wheels are used, the difficulty can only be got around by designs which are just as incorrect as the above. The application of an endless screw with one or two bevel gears seems to allow a greater freedom of arrangement, but up to now I have not seen an acceptable design of this kind. It seems that the idea has not been sufficiently studied.
The problem with it lies in the following circumstances: if winding is to be implemented with a moderate number of revolutions of the crown, then a very small wheel must be used on the barrel arbor in order to take up the effect of the screw; but then room for this screw must be found over or under the barrel, and the height of the work necessarily increases. If, in contrast, the wheel on the barrel arbor is large enough that the screw can mesh outside the extent of the barrel, then winding becomes so uncommonly slow that it requires gearing up.
160. Some time ago I made a number of keyless movements which had a more convenient layout of the train by using a rocking bar under the dial. The pendant is located at an angle of 45° from the centre of the barrel and the train wheels are of completely normal size. The 3rd wheel is fastened to the lower end of its arbor by a collet and moves in the area between the barrel cover and the lower barrel bridge. The gap is quite sufficient to have the barrel and the 3rd wheel completely free from each other. The centre wheel is attached in exactly in the usual way on the other side of the barrel. A work on this plan is not much higher than a key wound watch with a mainspring of the same width.
161. I still have to mention some other designs of keyless winding where the power is not provided at the pendant. There were some old watches which were wound by turning the case bottom. However, this was not followed up because of the impossibility of dust proofing such a case and because there is no method for hand setting in the usual way, i.e. with a key.
Other inventors had a circular rack operated by a slide protruding from the exterior of the case, and the watch was wound by moving the slide up and down. Still others used the action of opening the front cover of a hunter case to wind up a small part of the mainspring each time, and supported their idea with the fact that a hunter watch is definitely opened a certain number of times and so continues to run. It is not difficult to determine the value of mechanisms that justify their effectiveness by such statements. They are very similar to the old self-winding watch, which was wound by the movements made by the owner, and required him to walk or give it a prolonged shaking each day to keep it running. (17).
162. When designing a keyless mechanism it is essential to specify the relationship between the number of turns of the crown and those made by the barrel arbor. In the majority of carefully designed keyless watches each revolution of the stem causes about a 1/3 rotation of the barrel arbor. This is a relationship from which we should not depart too far in either direction. If a greater speed were given to the winding then it would be too difficult, especially for delicate fingers. If, in contrast, winding is divided over many rotations, then it will be very easy, but at the same time it will put too much power into the hands of the winder which could be fatal for the working parts if it is not used with the circumspection. Particularly at the end of winding there is danger for the stopwork, barrel teeth, centre pinion and so on. With a rocking bar the relationship between the number of rotations is simply the ratio of the tooth numbers on the winding pinion and the wheel on the barrel arbor, because there is direct transmission, tooth on tooth. In the other group of keyless mechanisms, which have gearing because the flat wheel is on the axle of the crown wheel, the relationship between the numbers of these two must be included in the calculation. For example, if the winding pinion has 12 teeth, the crown wheel 24, the spur wheel 40 and the barrel arbor wheel 60 teeth, then the ratio will be:
(12 x 40) / (24 x 60) = 1/3
and a revolution of the pinion causes a one third rotation of the barrel arbor.
163. There is still another danger which comes from roughly winding a watch that has a winding wheel with large and fine teeth in which the click operates. The excessive power which is often used for winding is suddenly halted by the stopwork. The stopwork is usually at the lower end of the barrel arbor so that a certain amount of torsion or coiling of the barrel arbor occurs and a further tooth of the wheel is forced past the click. From then on the watch runs under the influence of the full strength of the completely wound mainspring, increased by the reaction of the torsion which is transferred by the stopwork; the watch begins to overbank violently and often continues doing this for several minutes afterwards. This is accompanied by considerable danger to the escapement and, if no continuing damage is caused to the watch, then at least a major deviation in rate occurs. So a good keyless watch can show an excellent rate when well treated, but came into disrepute because of the irregular rate resulting from rough treatment when being wound.
164. A very simple means of overcoming this fault was probably first used by A. Lange. It consists of giving the click a certain amount of shake on its screw or stud. The recoil which comes from this shake is sufficient to reduce a torsion stress of the kind described above. Strangely, this mechanism was patented in the past year in England, when it had been used here for at least 15 years and put into circulation in many thousands of watches.
Occasionally I have made keyless watches with special clickwork under the large winding wheel on the barrel arbor and which fulfils this function well. The ratchet wheel is the same size as in a normal key wound watch but with rather wide teeth; the recoil caused by it is likewise sufficient to reduce the tension. There is plenty of room for this ratchet wheel and, if the tail of the click is made long enough, the mainspring can be let down without removing the barrel arbor wheel. Clickwork of this kind never annoys by getting in the way when fitting the movement into the case; whereas clickwork which is at the level of the winding wheels and on the edge of the largest one can create serious difficulties in getting it freely past the dome of the case.
165. If it can be avoided, the movement of a keyless watch should not be overloaded by the friction of redundant parts. Some watches are forced to drive one or two intermediate wheels and occasionally another pinion, and these are arranged in a way that does not reduce friction to a minimum. If their shoulder screws are overlooked when the repairer oils the movement, the friction will cause the watch to stop, particularly if the screw heads fit tightly in their sinks. All these parts should come into action only at the time of hand setting and afterwards move away in order to leave the motion work completely free. We must ensure that the hand setting wheel moves toward the centre of the minute wheel when it is brought into mesh. In addition, the teeth of this wheel should be cut thinly and pointed to avoid a sudden movement of the hands occurring when the wheels mesh and the points of two teeth meet.
166. The tooth profiles of winding wheels and pinions can be divided into two classes. One has the normal symmetrical profile while the other, which the Swiss prefer, has ratchet like teeth for the spur and bevel gears. There is no objection to the latter if they are well made, since these teeth act only in one direction, and the shape of the non working side of the teeth is arbitrary except in as far as it affects their strength. This form is necessary with the extremely thin winding wheels of many Swiss watches, but the front side of the teeth must be an involute and the back must be hollow only to the extent that it allows free movement of the meshed wheels. However, many of these wheels have such strangely formed teeth that it seems as if taste or fashion determined them.
We can make winding wheels with normally shaped teeth of appropriate thickness without fearing breakage. In this case the teeth should not be too fine and the flank and base must be shaped in such a way that they provide the greatest possible strength. They are kept short, which can be done because each tooth only works over a very small angle and then is replaced by another. The sides should not be parallel, but the gap should narrow towards the base; however the base should be rounded, in order to strengthen the tooth as much as possible.
167. With rocking bar winding the tooth pitch is, in most cases, prescribed by teeth of the minute wheel, and consequently finer teeth than desirable are used in many keyless mechanisms of this kind. If we fasten another wheel concentrically on the rocking bar wheel, which has the same pitch as the minute wheel and meshes with it, then we can get rid of this restriction and make the teeth of the winding wheels of any desired pitch. With all other winding systems we can select the tooth pitch as desired.
168. Steel is generally used for the winding parts and has no substitute for the arbors and pinions. However, where the wheels are concerned, in particular the larger of them, we might fear that their durability would be affected by hardening without any faults being perceptible to the eye. For this reason, for long a time I made them from aluminium bronze; however I stopped using this, not because it was unsatisfactory but because most of my customers preferred steel wheels.
169. Casing a keyless watch requires somewhat more work than one with key winding. The case pin must be put near the pendant, deviating from the usual rule (Art. 90), since otherwise we cannot put the movement into the case.
With the mechanisms where the hand setting parts are on the stem, it is best to make the stem and crown removable. These will be supported by a steel bridge fastened at the edge of the pillar plate while the inner pivot runs in a stud riveted to the pillar plate.
The winding pinion and ratchet must have only just sufficient clearance from the plate necessary for free movement, because otherwise they could shift when the stem is pulled out and re-insertion of it would be difficult.
In addition, this method makes case fitting much simpler and has the advantage that we can see the bevel gear in operation even when the watch is not in its case.
The crown is fastened in the usual way to the outer end of the stem and the stem is held by means of a screw, which goes through the side of the pendant and whose inner end fits in a grove in the stem. The screw head is sunk into the pendant so that it is flush with the surface.
With this arrangement we can remove the movement after the stem is pulled out just as easily as a key wound one. With hunter watches the stem must have a little movement along its length and the shoulder on the stem must not rest against the steel bridge, but be situated further out. The smaller part of the stem goes freely through a hole in the end of the case spring and the shoulder rests on the outside surface of the spring, so that we can cause the front cover to jump open with a pressure on the crown.
170. In most keyless watches the pusher for hand setting projects from the case band. With this method we must arrange the pusher so that the hole in the case through which it projects can be completely sealed. Usually this is done by a round pin with a button (Fig. 41) or a semicircular plate, half as wide as the band of the case and with its smaller half protruding from the edge of the case.
However, there are complaints about these protruding pushers. First it is possible that accidental pressure will engage the motion work and change the position of the hands, and under some circumstances the watch can temporarily stop. In particular, with the heavy and large link chains now used to carry watches, it is very likely that part of the chain will slip into the pocket and eventually press against the pusher. Furthermore it was objected that any lateral opening in the case should be rejected as it is an entrance for dust and impurities. Little weight should be put on this because a well implemented pusher will let extremely little dust through; probably none of us has found, in watches that have been carried for a long time, that the penetrated dust has come directly from there.
In addition, the protruding pusher was objected to on aesthetic grounds, because it gives an unacceptable asymmetry to the outside of the case. This objection is also insignificant.
171. But the united influence of these doubts produced a noticeable effort to create devices for hand setting without an external pusher; or, if a pusher had to be retained, to design it so that it is totally impossible for the watch to accidentally move into the hand setting position while being carried.
The first class of mechanisms has been discussed already (Art. 140 to 147). In the latter direction some recent inventions have achieved this purpose very well.
With hunter watches, some use the normal protruding pusher, but put a pin in it at right-angles; this pin extends upward through the case body and fits into a hole at the edge of the front cover. Hence, so long as the front cover is closed it is impossible to set the hands. Only after opening the cover can the pusher be pressed in and the hands set, and when the case is closed it is automatically secured again.
Other watches have the usual lateral pusher with a button (Fig. 41) and pressing it in is prevented by a protruding part of the front cover. After opening the cover this obstacle is removed, as already described.
One of the best solutions, in particular for open-face watches, is the following (already briefly mentioned in the Art. 143): A pipe is soldered into the case band at the appropriate place, so that it extends both outward and inward. The pusher is simply a smooth piece wire which fits into the pipe and whose exterior end is flush with the end of pipe. The pipe is provided with a slit which allows a fingernail to enter and press the pusher, while it remains unaffected by any other contact (Fig. 42).
172. The form of the crown is mainly a matter of taste. But those watches which require the crown to be pulled out to set the hands must have one that cannot be easily pulled out when winding the watch. With all other winding systems it is desirable to select the largest diameter of crown that will suit the work; not only because the best leverage is obtained, but also because the indentations of the crown are deeper and provide the fingers with an efficient grip, as well as offering a greater resistance to wear.
notes: 16 Grossmann is ignoring the necessity for friction. Without it screws would undo, nails fall out of wood and all machines and buildings would fall apart! [Trans]
17 The inadequacies of these old watches were remedied by A. v. Loehr of Vienna in very satisfactory way, so that they now begin to vie with the other winding systems. The details of them are given in my German translation of the great text book by Saunier.
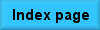
|